Supply Chain: Constant Change
There’s a patient at the end of every decision
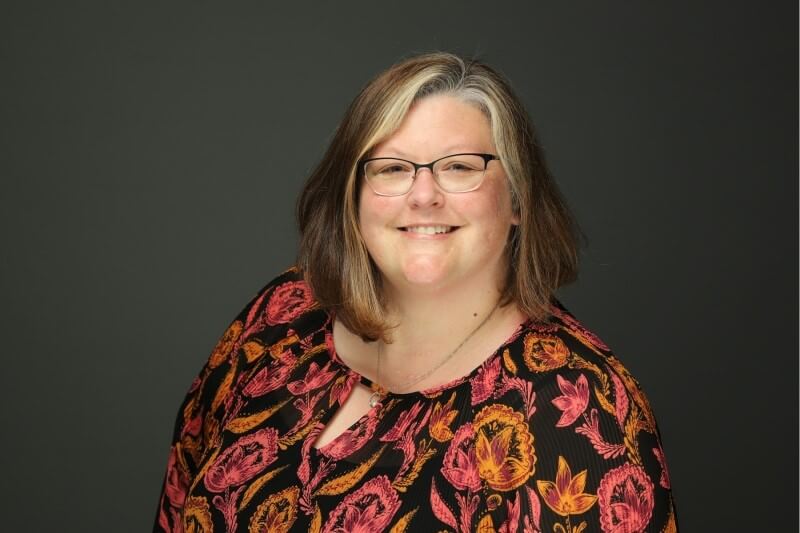
“We want Supply Chain to be like WiFi,” says Alyssa Kangas, Sr. Director, Contracting and Procurement. “That’s the vision – like when you walk into a building and your computer just connects to the internet. We want our caregivers to have what they need at their fingertips when they need it, without even having to think about it.”
That vision faced a number of challenges the last two years. Not only was the team in the middle of implementing an entirely new ERP system when the pandemic hit, but global supply chain disruptions have turned everything upside down.
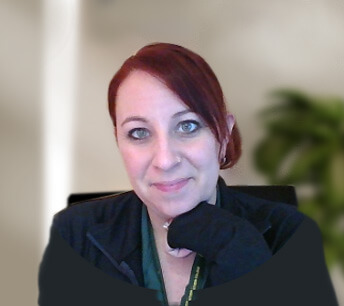
“The supply chain issues facing our team and the entire country still exist,” explained Kangas. “Many of our supplies are sourced from Asia, and factories aren’t operating at full capacity, if operating at all. Our world has not gone back to normal.”
Kangas acknowledges that it’s been two years with changes at every turn, including her team’s shift to remote working. While that alone was a big adjustment, there was an upside.
Regina Duval, Manager of Supply Chain Informatics, leads a team of four who she describes as stewards for supply chain data. “Our team is responsible for configuring, entering, editing and updating anything to do with item data, manufacturer data and supplier data,” she said.
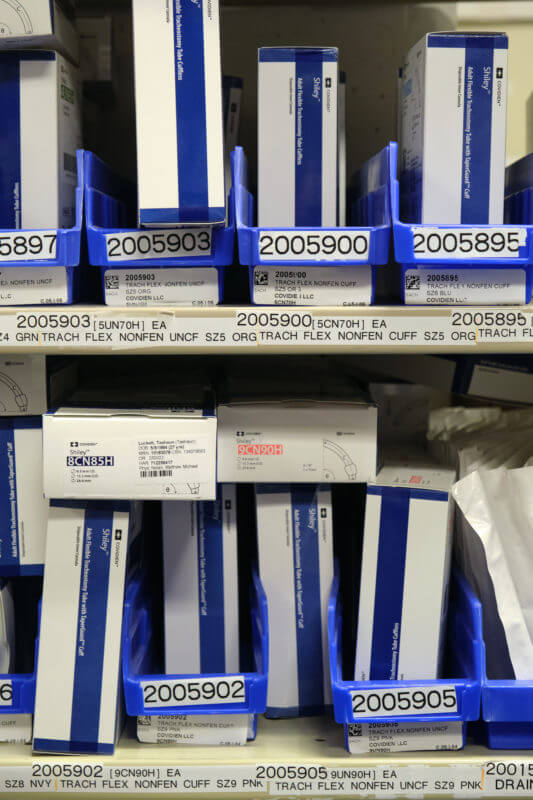
Distance makes the team grow stronger
Pre-Covid, Duval’s team was spread between St. Cloud and Willmar, so there was a natural physical division within the team. “When our teams started working remote, that division immediately went away,” she explained. “Everybody had to figure out how to communicate differently and now we have a Teams chat going 12 hours a day, because our team works flexible hours. We’ve gotten to know each other well and we just have an awesome team.”
Standardization has also helped.
“We handle 4.5 million data points, so there’s no way to juggle that much data effectively without having standard operating procedures (SOPs) for how everything gets entered. Establishing SOPs for everything has been our saving grace.”
The Procurement team is another group within Supply Chain that had to adapt how they worked together because their teams are spread across the region. “Geographically, it didn’t work out for us to get together and have that water cooler talk with everyone, every day,” said Kelsey Mitzel, Manager of Procurement. “When COVID forced us to work remotely, we put in place a structure for the virtual world and now we feel like one team. It’s actually made the team extremely close, regardless of geography.”
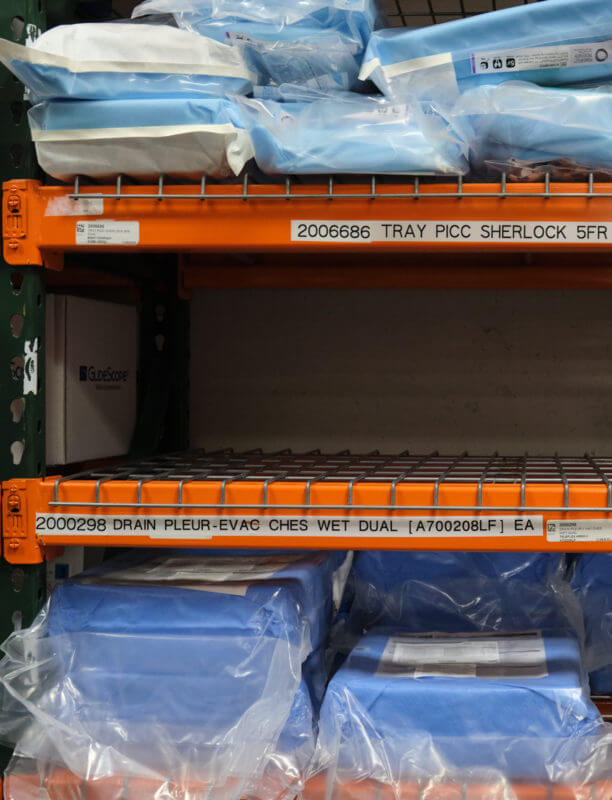
Connected to clinical teams
The pandemic changed how her team worked with departments that rely on them for the products they need to care for patients. Mitzel said the Critical Supply Management Committee was hugely helpful in making sure her team was closely connected with the clinical teams so that they understood their needs in terms of products and supplies.
“The committee started as a small group – maybe 5-6 people – but it kept expanding as more products and more departments became affected,” she said. “This group is now made up of about 50 people from different areas, so it provides an opportunity to hear any questions or product-related concerns directly from the care teams.
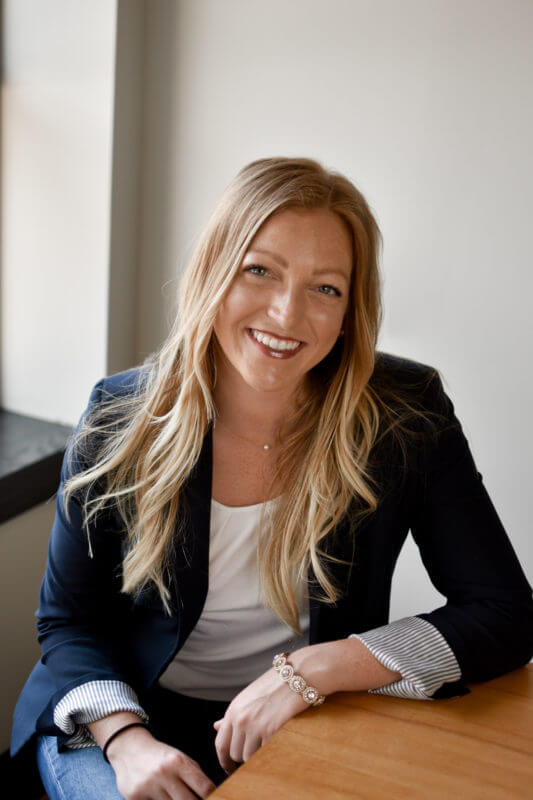
The committee has been a vital partner, especially as the Procurement team frantically sourced PPE supplies early in the pandemic. At times, this included resorting to the gray market, which is a marketplace where people who stockpiled supplies were reselling them at a premium price. “Committee members would help vet any products to make sure they met proper standards,” Mitzel explained. “We didn’t have a whole lot of success on the gray market and if we did, we would sometimes see things at a 3000% markup.”
For Mitzel, thinking about the past two years is also personal. “During the pandemic, my dad was diagnosed with stage 4 pancreatic cancer and he passed away about a year ago,” she said. “My family is from South Dakota so we were going to chemo appointments with dad at Sanford Health. Being on the receiving end of care during this time was eye opening because you could see how exhausted the nurses were and how understaffed the hospitals were.”
The experience made her grateful. “I’m very thankful for my team because they’ve had such a positive attitude about everything through challenging times.”
We know there’s a patient at the end of every decision that we make. I’m so grateful to be part of Supply Chain because of that.
Alyssa Kangas, Sr. Director, Contracting & Procurement
When Kangas thinks about her team of 32 people, she’s inspired by their dedication. “I’m just in awe of how the team has taken it one day at a time,” she said. “It’s a mindset of ‘we’re going to figure it out and we’re going to figure it out together.’ There are times it feels like we’re building the plane as we fly it, but everyone has been so dedicated to the purpose, recognizing what value they bring to the organization, and committing themselves to that. We know there’s a patient at the end of every decision that we make. I’m so grateful to be part of Supply Chain because of that.”